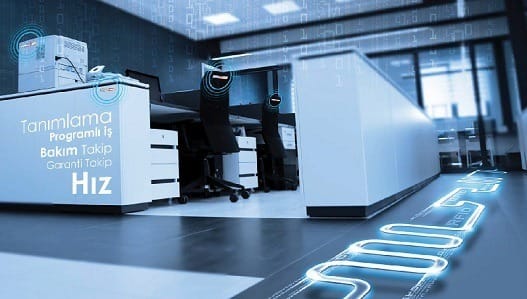
RFID asset tracking is a unique process of tracking business assets such as stock, equipment, and inventory through the use of RFID readers and tags.
An RFID (Radio-Frequency Identification) asset tracking system is a technology solution used to efficiently and accurately monitor and manage assets within an organization. This system utilizes RFID tags, readers, and a centralized software platform to streamline the tracking, location, and management of assets in real-time.
RFID asset tracking system is a technology solution used to manage and track physical assets within an organization. It utilizes RFID tags, which are small electronic devices containing a unique identifier, and RFID readers to automatically identify and track assets as they move within a predefined area.
Here’s how an RFID asset tracking system typically works:
RFID Tags: Each physical asset to be tracked is affixed with an RFID tag. These tags contain an embedded microchip and antenna which transmit data to RFID readers.
RFID Readers: RFID readers are installed at strategic locations throughout the facility or area where assets are being tracked. These readers emit radio waves and receive signals from RFID tags within their range.
Data Collection: As assets equipped with RFID tags move within the vicinity of RFID readers, the readers capture the unique identifiers from the tags and relay this information to a central database or software system.
Database or Software System: The collected data is stored in a centralized database or software system. This system may also include additional information about each asset, such as its location, status, maintenance history, and other relevant details.
Tracking and Management: Users can access the tracking system through a user interface to monitor the location and status of assets in real-time. They can also generate reports, set up alerts for specific events (e.g., asset movement, maintenance schedules), and perform other management tasks.
Benefits of RFID asset tracking systems include:
- Efficiency: RFID technology enables rapid and automatic data capture, reducing the time and effort required for manual tracking.
- Accuracy: RFID systems offer greater accuracy compared to manual methods, minimizing errors in asset tracking and inventory management.
- Visibility: Real-time tracking provides visibility into the location and movement of assets, allowing organizations to optimize asset utilization and prevent loss or theft.
- Automation: RFID systems can automate various processes such as inventory management, asset audits, and maintenance scheduling, leading to improved operational efficiency.
- Cost Savings: By streamlining asset management processes and reducing losses, RFID asset tracking systems can help organizations save costs in the long run.
Overall, RFID asset tracking systems offer an effective solution for organizations looking to efficiently manage and monitor their physical assets.
Quick Asset Identification
All the information needed by the users (product name, serial number, barcode number, brand, model, category, expiry date, warranty periods, invoice information, depreciation values, etc.) are recorded during the definition of fixtures in the system.
Creating a Sub-Asset List
Sub-products can be defined for each fixture, and sub-products are automatically embezzled and followed up with the relevant person while embezzlement transactions are carried out.
Photo Supported Recording
The photo of the fixture can be uploaded to the system via mobile hand terminal or application, product control is supported by visuals.
Debit Transactions
Fixed assets can be debited individually or collectively from a mobile handheld terminal or desktop application, either on an individual or departmental basis. Based on the embezzlement transactions carried out, an embezzlement receipt can be printed through the system. Thanks to the flexible debit slip design feature, special debit slip designs are created for companies.
Online Debit Tracking
All users can access the embezzled fixed assets list online via the MetaMatik web interface.
Operations
All fixtures whose warranty period is approaching or past can be filtered according to the criteria set by the users. Necessary measures are taken before the warranty period of the fixtures expires
. Fixtures sent for repair and returned from repair are followed up. Users make plans for fixtures that require calibration and routine maintenance, and the system monitors them. The system notifies the users of the fixtures that are due for maintenance and calibration by mail.
Invoice Tracking
Invoices belonging to fixed assets can be archived in the system. In ongoing purchases, the process can be followed via Meta-Matik without the need to examine the accounting records.
PERIODIC OPERATIONS OF FIXTURES ARE AUTOMATICALLY FOLLOWED!
Consumable Tracking
Appears to be small; However, consumables, which take a serious place in operating expense items, are taken under control from the system. The system automatically alerts users to purchase when consumables fall below the predefined control level. Thus, disruptions caused by lack of stock are prevented.
Online Demand Management
All authorized users can request online fixtures through the MetaMatik web interface, and can also monitor their demand processes online. Barcode and RFID can be transferred to the RFID system, with the information of the existing barcode system on the same platform. In addition, thanks to the barcode and RFID supported mobile hand terminal, asset tracking can be started with a barcode and switched to RFID tags at any time.
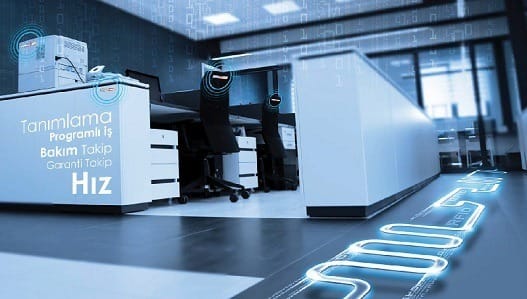